News
Maker’s Mark: Log Stack Cabinet
Designer-maker Charles Byron, one half of duo Byron & Gomez, answers questions about his Bespoke Guild Mark awarded piece, the Log Stack Cabinet.
Name of piece: Log Stack Cabinet
Designer name: Charles Byron
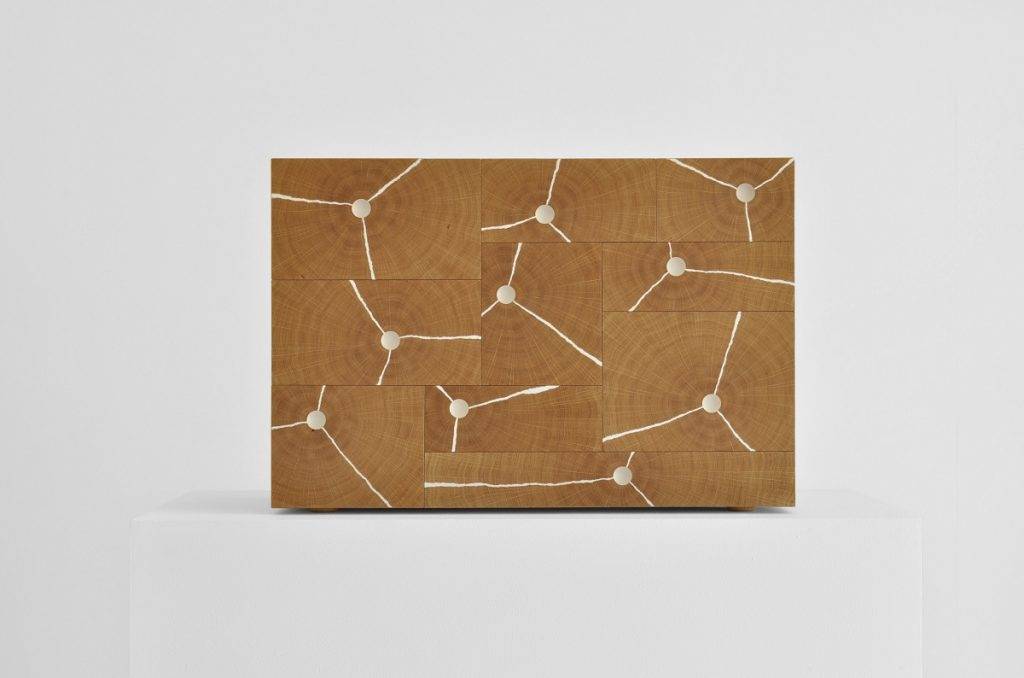
Can you tell us the background of this project and your inspiration to make it?
What I really wanted to do with this piece is show off the beauty of end grain. It’s an aspect of wood that is so often hidden away yet to me it is every bit as stunning and deserves to be shown off. Everything about the log stack cabinet revolves around showing end grain at its best.
Please explain the materials you used for the piece and why they were chosen over others.
With end grain in mind I was delighted when I discovered that I could source large leaves of true end grain oak veneer, as apposed to oysters. I based the whole project around this veneer and what I could do with it. I really wanted to create the look of having sliced cleanly through a tree, showing the full circle of growth rings. The veneer came as two stacks of consecutive half circles but due to shrinkage and the inevitable breakage of the fragile, crumbling edges it was not possible to simply join the two leaves back together. I had to introduce a third leaf which came from the next layer of veneer so the rings wouldn’t line up. That leads me to the other main material in this project, white resin. The white resin fractures were my way of distracting the eye from the fact that the rings didn’t line up, creating that slice of tree illusion that I was after.
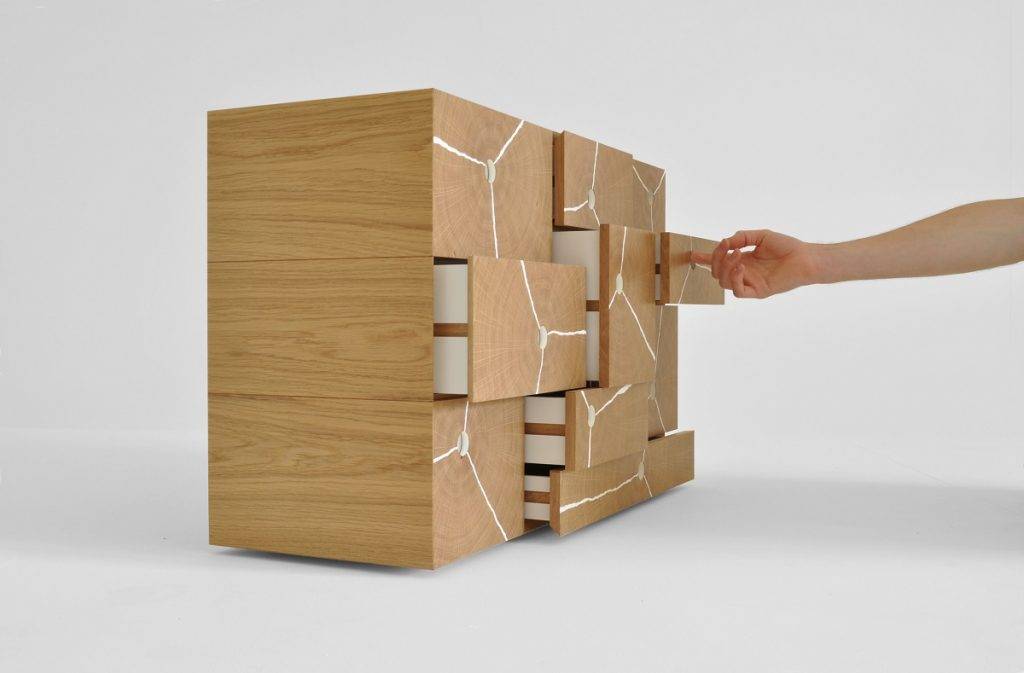
What features – subtle or obvious – are you particularly proud of/make the design unique?
It’s undoubtedly the use of end grain that makes this project unique but the supporting act that often goes un noticed is the grain direction on the carcass. Using one piece of crown cut oak per drawer front I ran the grain front to back, lining up the crown with where it would be if the front and side where two aspects of one solid block of wood. It’s not something that jumps out at you but it helps to sell the whole illusion.
How long did it take to create, from initial design to completion?
In all honesty I don’t know. I was a student at the time I made it and I wasn’t very good at recording my hours back then. It took a long time, that much I can say for sure. There were some quite repetitive tasks involved but I guess that’s just good practice when you’re learning.
What modifications did you make along the way and why did you make them?
None at the time. Some designs go through a lot of iterations and get repeatedly tweaked as I make them but this is one of those ones where it pretty much ended up looking like the first sketch I ever did but I have since made a base for it to make it a floor standing piece. I felt this would make it easier to place in a house rather than a gallery.
What was the most challenging aspect of the design?
Working with the end-grain veneer presented some unique challenges that had to be overcome. It’s quite fragile and doesn’t stick down as well as normal veneer. It’s also very porous so bleed through is an issue. You have to work very quickly when you press it as the moment it makes contact with the glue your nice flat piece of veneer tries to turn into something resembling an ice cream cone.
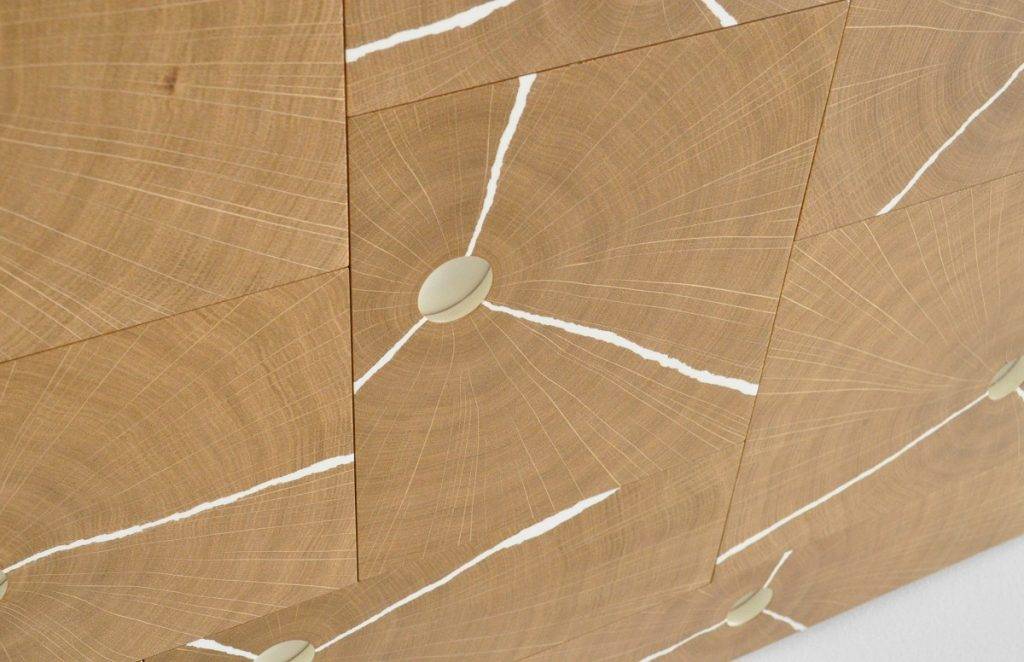
What does the Bespoke Guild Mark mean to you?
I was absolutely blown away to get it. As this was a student piece and I was making a bit of a life change to study furniture making it was a real vindication that this was something I could make a success of.
What do you see as the benefits of being awarded a Bespoke Guild Mark?
For me it really opened a lot of doors. I was only just starting out and I was being invited to exhibit along with all these fantastically talented and long established Guild Mark holders. The Furniture Makers’ Company is a fantastic organisation that really supports makers and I’m grateful to be affiliated with it through the Guild Mark.